Identifying and overcoming current challenges in warehouses and Distribution Centers
Warehouse and logistic centers owners face a constantly evolving environment, marked by fluctuating demands, supply chain pressures, and ever-increasing customer expectations. In this era of e-commerce and fast delivery, the ability to identify and overcome operational challenges is essential for the success of any business. Through this article, we aim to explore the most common issues currently facing the intralogistics industry, providing you with concrete solutions to navigate this complex environment with ease.
As previously mentioned, warehouse owners and logistics center managers frequently encounter a range of challenges that can impact the efficiency and profitability of their operations. Some of the most common issues include:
1. Insufficient storage capacity:
Rapid accumulation of inventory can become a significant bottleneck, hindering efficient stock management and timely product retrieval. This typically leads to wasted time, increased operational costs, and even customer dissatisfaction due to shipping delays. To address this, warehouse operators can choose to optimize existing space by utilizing appropriate storage systems tailored to the types of stored goods, by reorganizing the existing shelving layout or modifying existing shelves with more space-efficient storage solutions.
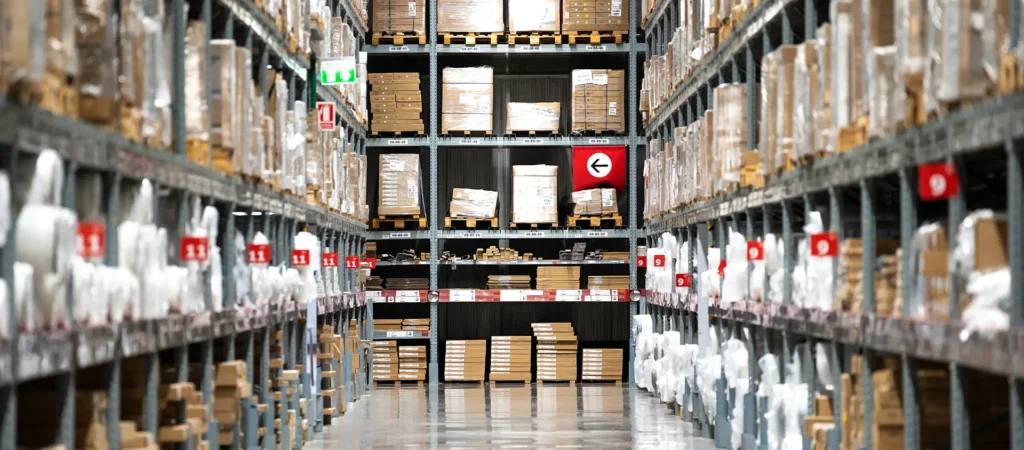
In terms of the diverse range of racking solutions available on the market, we offer pallet racking systems (Heavy Duty, Drive-In, Push-Back, Roller Push-Back, or Gravity Flow) as well as lightweight shelving (such as Carton Flow gravity shelving, archive shelving, or HACCP-certified stainless steel shelving for the food industry). Additionally, our portfolio includes racking solutions for atypical products, perfectly tailored to accommodate goods of any shape, size, or weight, optimizing storage density and accessibility within automated warehouse environments.
As the need for increased storage density and space optimization becomes increasingly common for warehouse owners (especially with the growth of e-commerce), solutions such as mezzanine platforms, multi-level mezzanine racking structures (up to 3 levels), and mobile racking systems (manual, electric, or remote-controlled) are gaining popularity. These mobile racking systems can be used for both pallet storage and archiving or light-duty storage, providing versatile and efficient storage solutions for modern warehouses.
As rack reconfiguration is also considered a viable solution for storage optimization, pallet racks or light-duty shelving can be installed in a back-to-back configuration (ideal for storing high-volume, low-variety products).
Therefore, whether you need a reorganization of existing racking or a new racking system, the ideal solution undoubtedly exists for every warehouse. However, it must be carefully selected based on the desired load capacity, dimensions of stored goods, method of goods access, handling method, availability, level of accessorization and modularity.
2. Inefficient inventory management:
Inventory discrepancies can lead to financial losses, stockouts, and customer dissatisfaction. Implementing a Warehouse Management System (WMS) with real-time inventory tracking and reporting capabilities can significantly improve accuracy and efficiency.
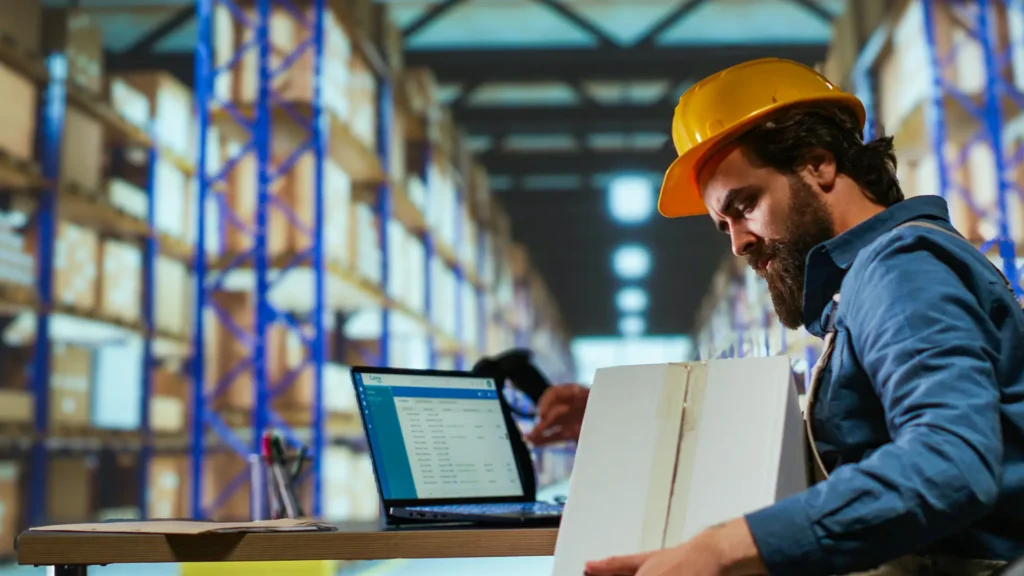
3. Security Challenges:
Warehouses are frequently targeted for theft and vandalism. Implementing advanced security systems, including surveillance cameras, alarms, and access control, can deter potential criminals. Additionally, establishing strict security protocols for employees, especially those involved in automated processes, is crucial for maintaining a secure environment.
4. Accidents and Safety Issues:
Workplace accidents can lead to serious employee injuries and financial losses for the company. Ensuring proper safety training, choosing appropriate safety solutions, demarcating warehouse areas with signage solutions, adhering to safety regulations with the help of accessories, and using personal protective equipment (PPE) are essential for preventing accidents.
5. Shortage of Skilled Labor:
Attracting and retaining qualified personnel can be a significant challenge, impacting operational efficiency. Investing in training and professional development programs, offering competitive salaries and attractive benefits, and fostering a positive work environment can help attract and retain skilled employees.
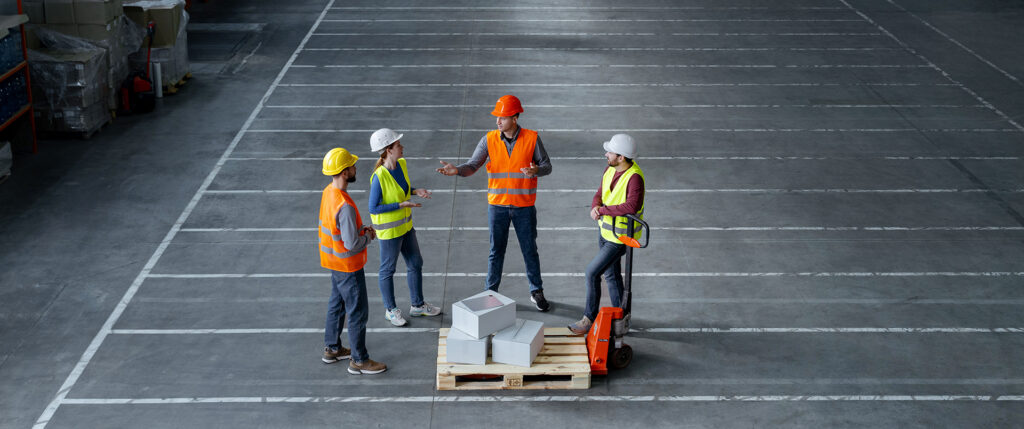
6. Delivery Delays:
Delays in order processing and shipment can negatively impact customer satisfaction and damage the company’s reputation. Optimizing picking and packing processes, utilizing a Transportation Management System (TMS) for delivery planning and tracking, and partnering with reliable carriers can help mitigate delays.
7. High Operating Costs:
Expenses related to energy, maintenance, labor, and equipment can significantly impact profit margins. Implementing energy-efficient measures, negotiating better contracts with suppliers, and optimizing processes to reduce waste and unnecessary costs can all contribute to lowering operational expenses in warehouse and automation settings.
8. Equipment Maintenance:
Malfunctioning or worn-out equipment can lead to operational disruptions and increased repair/replacement costs. Implementing a preventive maintenance program (e.g.: EUROFIT SIGMA) is crucial to ensure optimal equipment performance and prevent unexpected breakdowns.
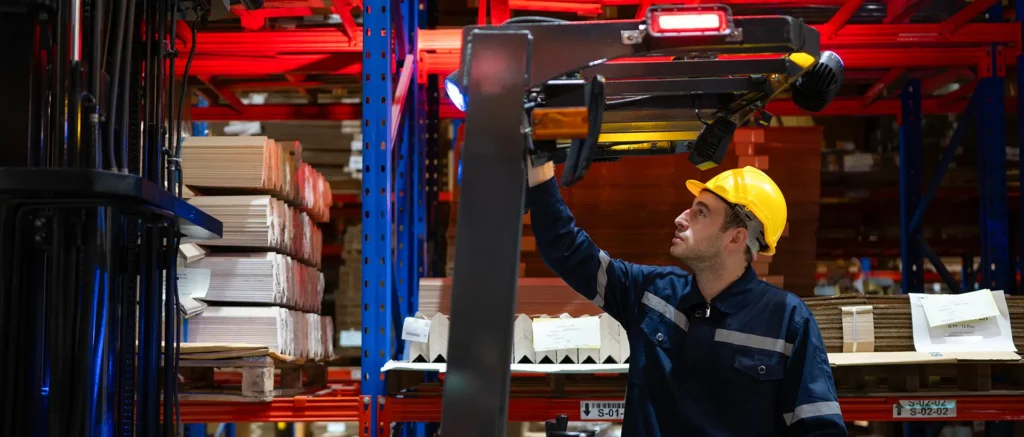
9. Returns Management:
This process can be complex and significantly impact inventory management and profitability. Establishing a clear and efficient returns management process is crucial, encompassing inspection, refurbishment, restocking, or disposal of returned items. Leveraging warehouse automation technologies, such as automated sorting systems and AI-powered inspection tools, can streamline this process, reduce manual errors, and optimize inventory levels.
10. Ineffective Internal Communication:
Poor communication between departments can lead to confusion, errors, and decreased productivity. Implementing a centralized communication system and regular team meetings can streamline information sharing and ensure everyone is aligned with common goals.
11. Lack of automation when the situation demands it:
In an era of accelerated technological progress, manual management of the logistics flow can be a significant obstacle to a company’s efficiency and competitiveness. Automating and robotizing processes such as receiving goods, warehousing, picking, packing and shipping can bring substantial benefits. Autonomous robots can efficiently navigate warehouses, handle goods with precision and speed, optimize space utilization, and significantly reduce human error. Integrating robots into the logistics flow can lead to increased order processing speed, reduced labor costs, and improved customer satisfaction through faster and more accurate deliveries. Ignoring the potential offered by automation and robotization means falling behind competitors who adopt these innovative technologies.
By proactively addressing these challenges, warehouse owners and logistics center managers can improve operational efficiency, reduce costs, and increase profitability. Implementing appropriate storage systems, such as automated storage and retrieval systems (AS/RS) or high-density racking, improving the picking process by implementing GTP (Goods-To-Person) systems, investing in employee training and automation technologies like robotics or AI-powered optimization software, and fostering a safe and productive work environment are crucial steps in overcoming these common issues.
In addition to these aforementioned challenges, there are further aspects worth considering when discussing the challenges of the logistics environment, namely:
Technology Integration: Outdated or disjointed IT systems can hinder inventory management, order tracking, and interdepartmental communication. Investing in modern technology solutions, such as warehouse management systems (WMS) and automation solutions, can streamline operations and enhance business performance.
Sustainability: Warehouses and logistics centers can significantly impact the environment due to high energy consumption and waste/emissions generation. Implementing sustainable practices like energy-efficient lighting, recycling programs, and eco-friendly packaging can reduce these facilities’ ecological footprint.
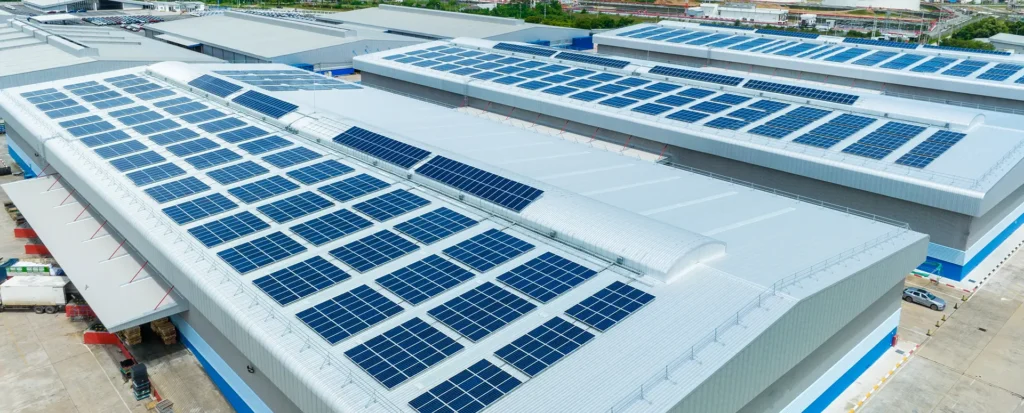
Regulatory Compliance: Warehouse operations are subject to various regulations and compliance requirements, such as safety standards, labor laws, and environmental regulations. Ensuring compliance with these regulations is crucial to avoid penalties and maintain the company’s reputation.
Supply Chain Disruptions: External factors like natural disasters, political instability, or global pandemics can disrupt supply chains and impact warehouse operations. Developing contingency plans and building resilient supply chains with diversified suppliers and transportation options can help mitigate the impact of such adverse events.
Customer Expectations: Today’s customers have high expectations regarding order fulfillment, delivery speed, and transparency. Meeting these expectations requires efficient order processing, accurate inventory management, and effective customer communication throughout the fulfillment process.
Whether you need storage solutions, automation systems, or maintenance services, EUROFIT specialists will help you adapt to the ever-changing needs of your customers and the logistics industry.
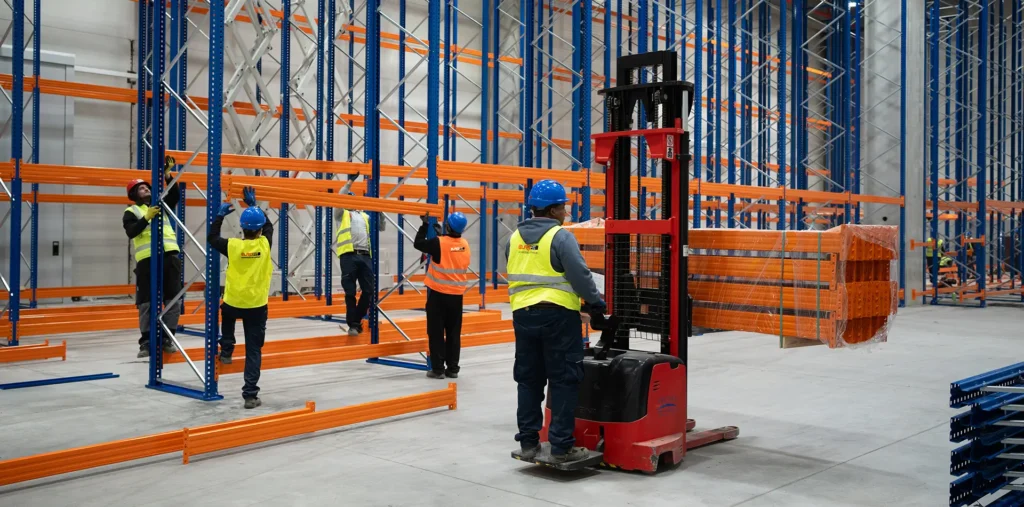