AGV vs AMR
Is an AMR the same as an AGV? The short answer is no. So what are the differences?
First, let’s look at what these acronyms mean. An AMR (Autonomous Mobile Robot) is, as the name implies, an autonomous mobile robot, whereas an AGV (Automated Guided Vehicle) is an automated guided vehicle. Although an autonomous mobile robot sounds very similar to an automated vehicle, the two differ in some very important ways.
AMRs are autonomous, which means that they move, “think” and plan their own routes. AGVs, on the other hand, are guided, so they travel on fixed routes using magnetic tape, painted markings, stickers, QR codes or laser targets.
The best analogy is that an AGV is like a locomotive, limited only to running on its tracks, while an AMR is like a taxi, able to move freely between any two points and replan the route when traffic density is too high. The purpose of both means of transport is the same, but the mode is different.
AMRs can operate in almost any storage space without the need for pre-installed guidance systems. They move on their own thanks to built-in intelligence and can adapt to changes in warehouse layout. Ease and speed of deployment is a plus – without requiring special equipment, AMRs can be up and running as soon as they arrive in your warehouse. AGVs, on the other hand, require the installation of guidance systems, and no matter how hard you try to maximise efficiency, there may still be inaccessible areas due to the warehouse structure or floor.
AMRs can be deployed in warehouses of any size and configuration and can easily adapt to changes in the environment with the help of automated technology. AGVs are also flexible, but require more effort to adapt to changes around them. Because they rely on sensors and GPS systems for navigation, AGVs can be disrupted by changes in the environment, such as the addition of new equipment to a warehouse. So if you want to change the warehouse layout, you have to reprogram the AGVs, which can cause disruptions in daily operations.
With the flexibility of mobile robots to reach any point and their ability to change their route and make decisions autonomously, AMRs significantly increase the efficiency of picking operations, with increases of up to 3 times or more. In this respect, AGVs are more limited. However, where the robot is required to move along a fixed route, AGVs can achieve similar levels of productivity as AMRs.
Because AGVs can move both horizontally and vertically, like a forklift, they can be used to handle large loads and have the ability to reach greater heights of up to 3000 mm. Although AMRs with a lift function are also available, the maximum extension height is 355 mm and the maximum transport load of AMRs is also much lower. While AGVs can carry up to 3000 kg, most AMRs carry up to 600 kg.
However, because AMRs can move around people and obstacles, they are considered safer than AGVs. AGVs often operate in areas separated from people to maintain safety.
These factors make guided vehicles very predictable and their actions can be planned. That’s why AGVs are punctual and very efficient in performing transport tasks.
On the other hand, the movement trajectory of AGVs is often more difficult to predict due to their autonomy. People cannot predict how they will overcome obstacles or which new routes they will take. So when it comes to predictability and reliability, AGVs offer an advantage.
At first glance, the cost of buying an AGV is usually lower than that of an AMR, which costs more due to its artificial intelligence and built-in sensors. However, once the cost of modifying an entire warehouse to accommodate an AGV, including more complex planning and maintenance, is taken into account, the costs start to differ.
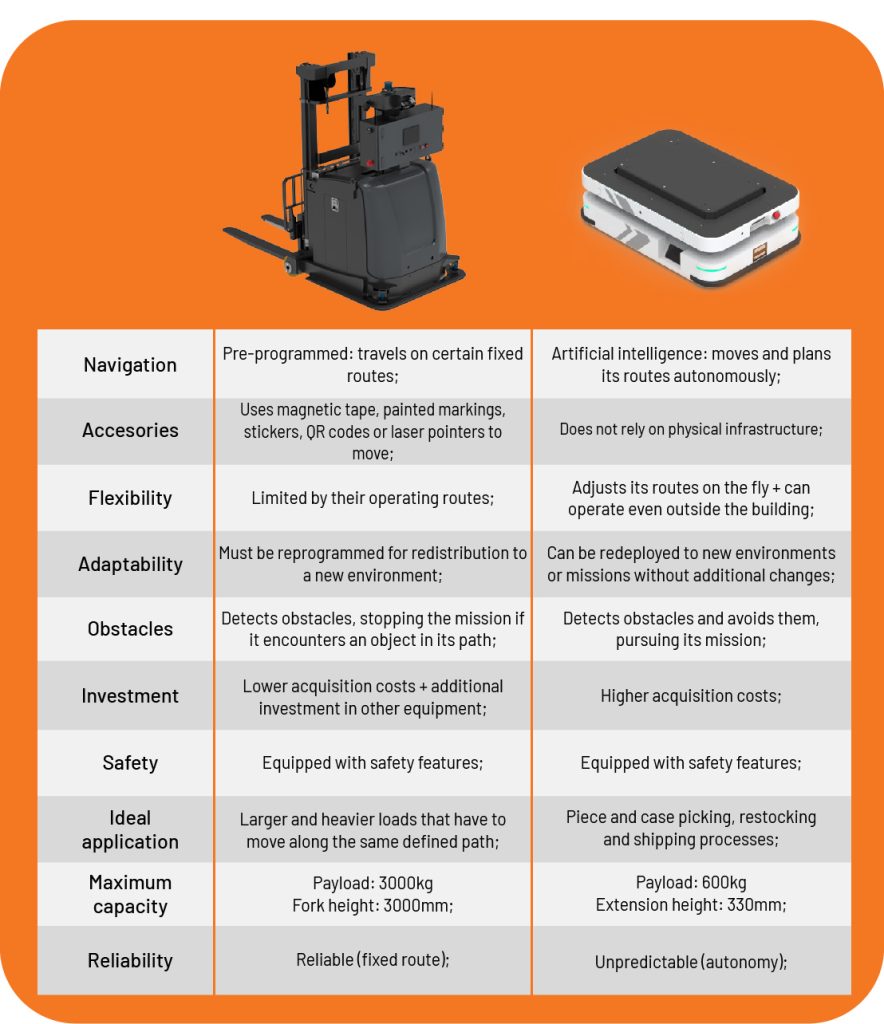
Ultimately, choosing between an AMR and an AGV comes down to understanding the specific needs of your warehouse and business. It’s important to evaluate factors such as workflow complexity, warehouse configuration, future business projections, the level of adaptability and flexibility required, the nature of the tasks you want to automate, and your budget. If your transportation routes remain the same, your material flow is steady and voluminous, and the number of obstacles is low, then an AGV is the best choice. They are less expensive and perform all their tasks with accuracy and reliability. However, if the route and transport tasks change over time, then AMR is definitely a more suitable choice.
AMR is the best choice for collaborative human-machine picking operations in warehouses. Highly scalable and adaptable to different situations thanks to a large number of functional modules, AMRs are suitable for picking tasks, pallet handling and more.
Although AMRs and AGVs may look similar, they are significantly different and often have different uses. In general, AGVs are more efficient for less complex tasks, such as transporting raw materials in receiving, warehousing or shipping processes, but always with pre-defined tasks and routes. AGVs are also ideal for bulky palletized goods.
By considering these factors and balancing the pros and cons of automation solutions, you can make informed decisions that will help you optimize your material handling operations. Using our expertise, we can work with you to find the ideal solution and increase the productivity and profitability of your business.