Don’t let the cold freeze your business
In the age of technology and continuous innovation, automation has become a cornerstone of many industries and sectors. Among these, cold storage facilities have become increasingly reliant on automated systems to efficiently and accurately carry out their tasks.
Traditionally, cold storage facilities depended heavily on manual labor, which entailed higher risks of human error, inefficiencies, and delays in handling and storing perishable goods. However, with the advent and adoption of automation technology, cold storage facilities have undergone a significant transformation.
Cold storage automation involves the implementation and use of computer-controlled systems and equipment, such as robots, sensors, sorting machines, and specialized software, to manage and optimize operations. Automated systems can precisely manage product flow and perform sorting, storage, and shipping operations far more quickly and efficiently than manual labor. This results in reduced operational costs, increased productivity, and improved customer satisfaction through the timely and accurate delivery of requested products.
In summary, cold storage automation represents a crucial step in the evolution of the food industry and the supply chain. By leveraging automation technology, cold storage facilities become more efficient, accurate, and adaptable to the ever-changing demands and needs of the market.
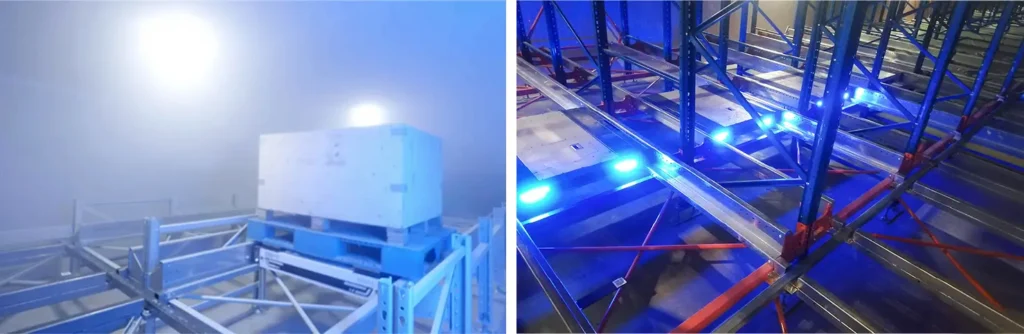
Challenges of automated cold storage
Due to the unique characteristics of cold storage environments, new technologies are needed to bridge the gaps in the automated solutions currently available on the market. It is preferable that the technology utilizes off-the-shelf components and modularity to enable rapid installation and commissioning for faster return on investment.
Implementing cold storage automation presents several challenges, but we at EUROFIT are here to help you achieve a smooth and successful transition:
- Challenge (C): Limited storage space.
Solution (S): Maximum density storage in limited spaces for minimal thermal losses. - C: Harsh working environment – employees need improved workplace safety, especially those working in sub-zero temperatures.
S: No employees need to enter the sub-zero environment of frozen storage facilities. - C: High energy costs – automated devices typically consume large amounts of electricity.
S: Due to high storage density, our solution significantly reduces the energy consumption required for cooling in cold storage facilities, compared to using conventional forklifts or forklift-based warehouses. - C: High initial investment – implementation costs can be substantial, making it difficult for some organizations to justify the investment in the short term.
S: The return on investment (ROI) for this automation system is estimated at 1-3 years. - C: Complex implementation – comprehensive planning and coordination are required to ensure successful implementation.
S: Implementation is straightforward due to the intelligent design of the entire structure. - C: Maintenance and support – requires regular maintenance and support to maintain proper operation.
S: The Intelligent High-Density 3D Shuttle system requires minimal maintenance.
Intelligent High-Density 3D Shuttle
The Intelligent High-Density 3D Shuttle system is a next-generation solution for pallet storage in conventional and cold storage warehouses. With equipment specifically adapted to your warehouse’s conditions, it offers advantages such as high-density storage at low temperatures, flexibility, and scalability. The system combines a robotic platform and intelligent software with an AI algorithm.
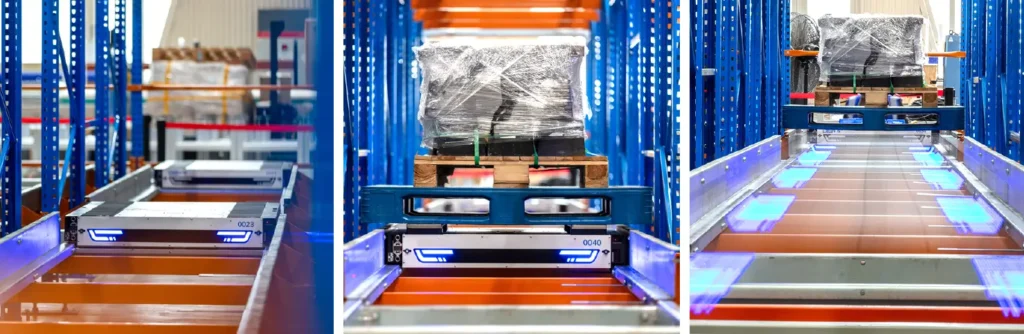
Application scenarios
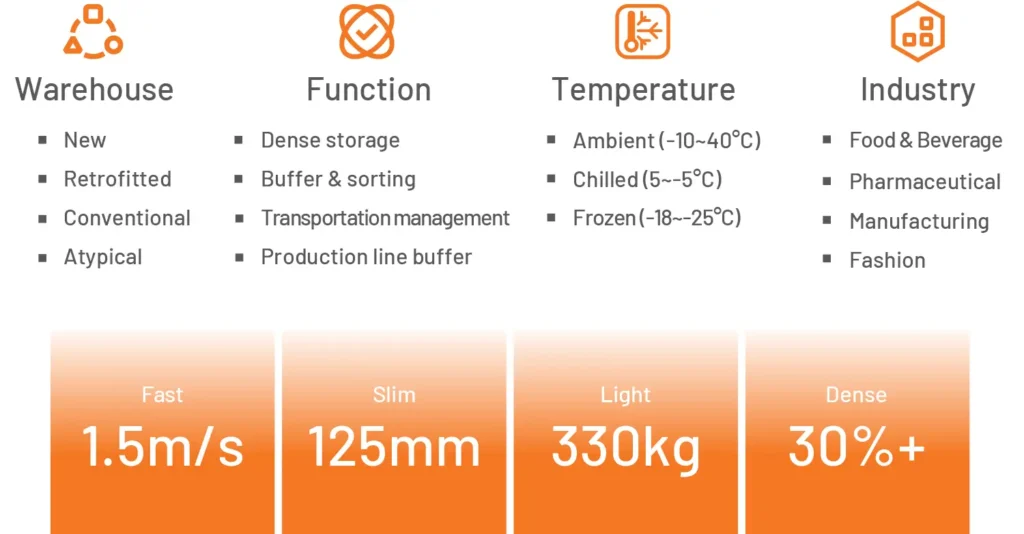
About the Intelligent High-Density 3D Shuttle System
The Intelligent High-Density 3D Shuttle system enables warehouses and factories to leverage the benefits of automation for storing and retrieving palletized goods (AS/RS). The system organizes and optimizes your warehouse so you don’t have to, seamlessly integrating with existing ERP systems and processing lines to accept pallets without manual intervention.
Increased capacity: Maximize storage density and optimize warehouse space utilization.
Increased productivity: Fluidizați operațiunile, reduceți munca manuală și îmbunătățiți randamentul.
Automation provides solutions to a range of challenges faced by today’s warehousing professionals. Designed and supported by industry-leading talent in software development and mechanical engineering, our system offers both redundancy and scalability. We leverage automation to eliminate overhead costs in the warehousing environment, reducing heat loss, labor costs, and general expenses, while transforming productivity and efficiency into the core of your business.
5 elements = your business success
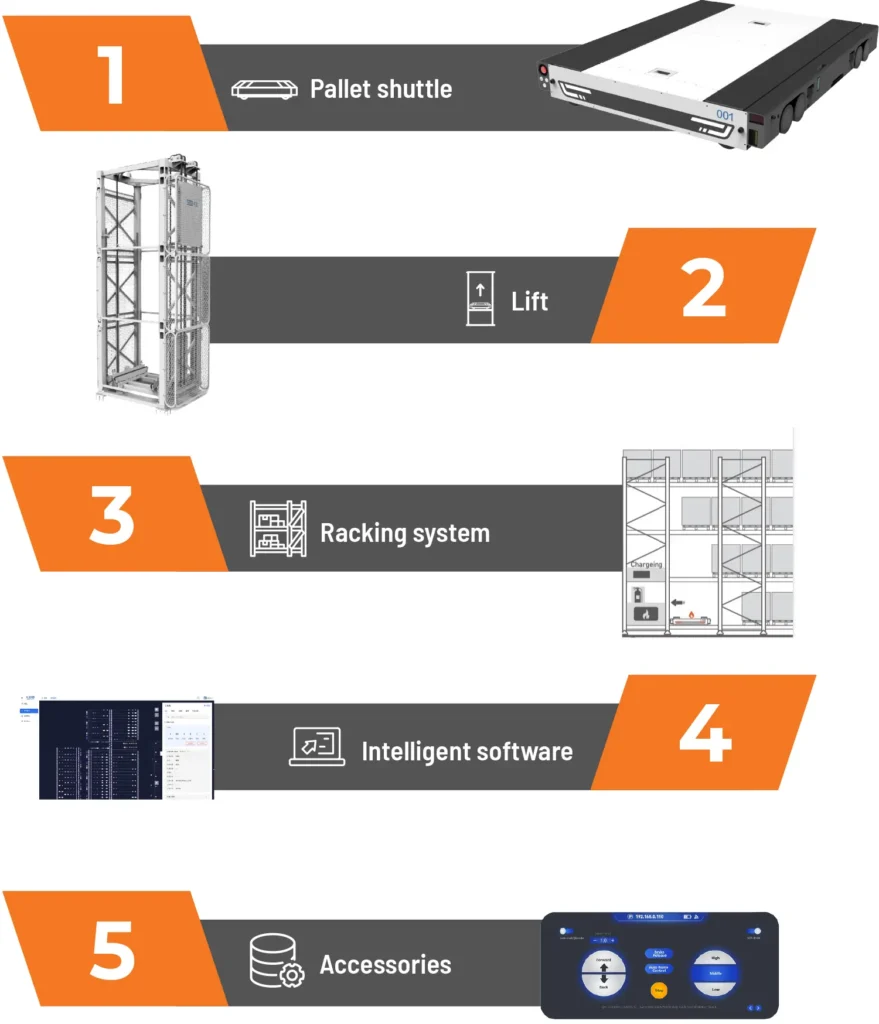
System components
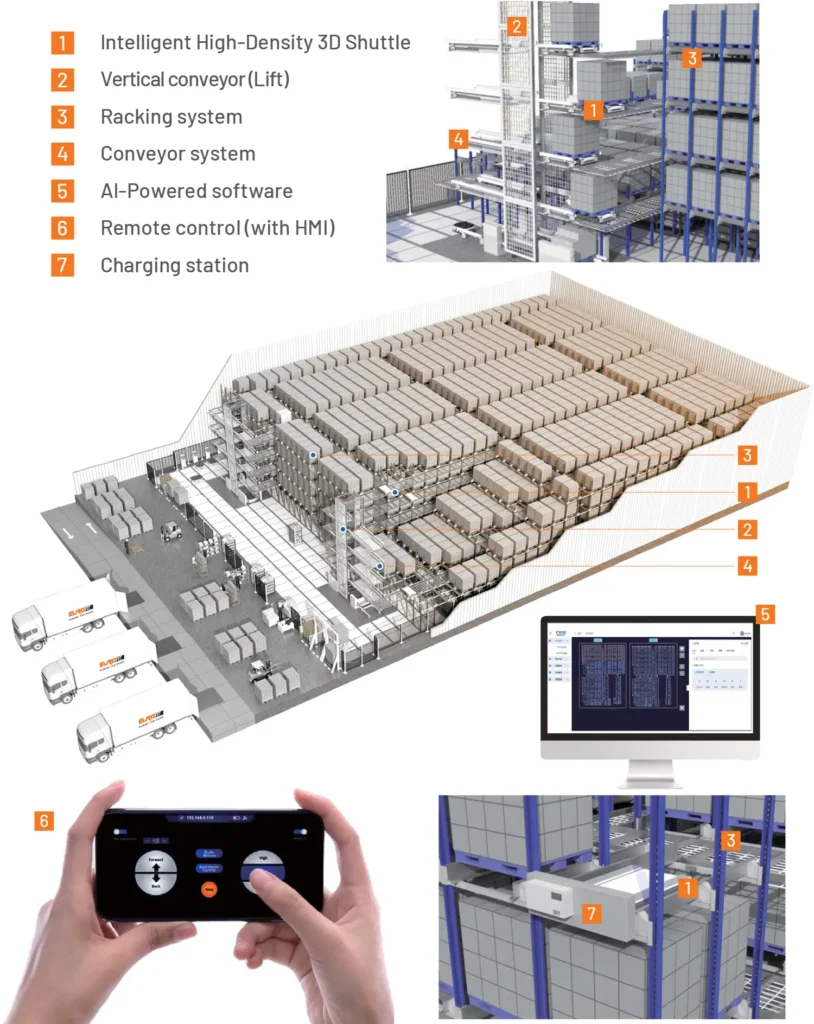
Benefits of the Intelligent High-Density 3D Shuttle System
- Maximum storage density: Optimizes space utilization within your warehouse.
- Efficient and ergonomic order picking: Streamlines picking processes and reduces operator fatigue.
- Reduced handling: Minimizes manual intervention, improving accuracy and speed.
- Secure pallet handling: Ensures safe and reliable pallet movement throughout the system.
- Reduced labor requirements: Decreases reliance on manual labor, lowering operational costs.
- Time efficiency: Accelerates storage and retrieval processes, improving overall warehouse throughput.
- Full scalability: Easily expand the system by adding more shuttles and racks as your needs grow.
- Built-in redundancy: Ensures continuous operation even in the event of component failure.
- Low energy consumption: No heavy machinery counterweights or warehouse lighting needed, reducing energy costs.
- Turnkey solution for existing warehouses: Seamlessly integrates into your current facility.
- Enhanced pallet safety: Minimizes the risk of pallet damage during storage and retrieval.
- Optimized storage process: Improves inventory organization and accessibility.
- Zero risk of rack damage: The shuttle system operates without causing damage to storage racks.
- Interconnected rack structure: Provides enhanced stability and safety for stored goods.
- Super-flat floor not required: Adapts to existing warehouse floor conditions.
- 20+ year lifespan: Offers a durable and long-lasting solution for your warehouse.
- Reduced warehouse traffic: Improves safety by minimizing forklift and personnel movement.
- Multi-level storage: Maximizes vertical space utilization in your warehouse.
- Integration with your ERP system: Streamlines data exchange and inventory management.
- Integration with your processing lines: Connects seamlessly with your existing production processes.
- Built-in automated inventory management (FIFO/LIFO) and warehouse management solution: Provides comprehensive inventory control and optimization.
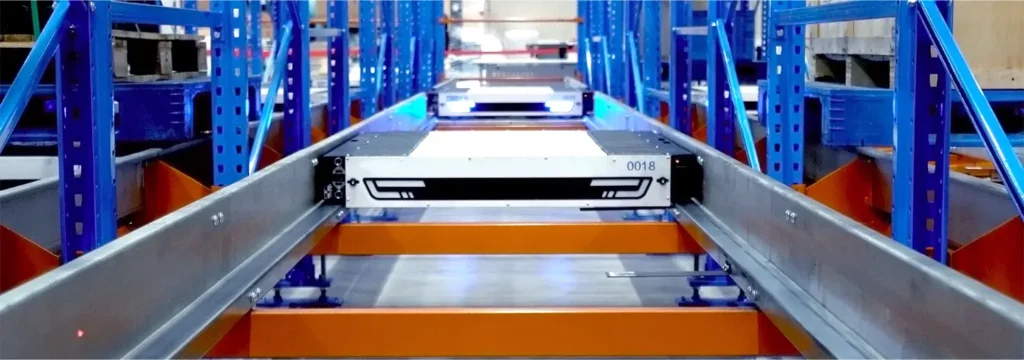
Increased capacity
Our patented picking tunnel allows clients to truly maximize their warehouse space. We utilize all density above the picking aisle, recognizing this area as valuable storage.
Warehouse Safety
The seamless integration of storage spaces, warehouse structures, and management software prioritizes the health and safety of your employees. Each project is tailored to our clients’ operational requirements, continuously identifying ways to enhance working conditions and productivity. Our critical approach to safety ensures that an automated warehouse is feasible for any industry.

Advantages of cold storage automation
- Increased Density
• The 3D pallet shuttle system ensures maximum storage density within limited cold storage areas.
• Reaches heights of up to 25 meters, enabling better space utilization.
• Increase storage capacity by over 30% compared to traditional forklift storage. - Reduced Energy Consumption
• Reduces energy consumption used for cooling individual pallets by 30% and lowers CO2 emissions.
• Consumes 50% less electricity compared to a conventional forklift or forklift warehouse.
• Carbon offsets reduce costs by helping to decrease carbon emissions. - Enhanced Efficiency
• Fully automated operation is possible 24 hours a day, 365 days a year, even in extremely cold environments of -25°C.
• 50% more efficient handling. - Assured Safety
• Ensures the safety, comfort, and health of your employees.
• CE-certified products, compliant with EU safety standards, promote a safe working environment. - Intelligent Operation
• Reliable, efficient, and equipped with features to maximize uptime and minimize downtime.
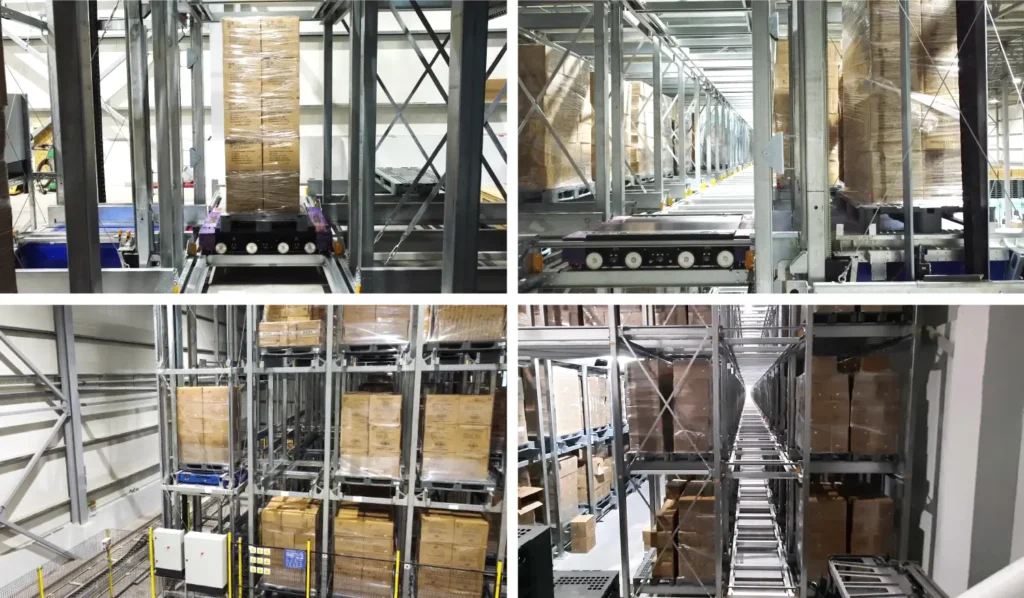
Other cold storage automation solutions
- Stacker Crane System: Engineered for automated material storage. These cranes move within the warehouse along designated aisles, precisely positioning themselves to retrieve and store materials. Stacker cranes are guided by a Warehouse Management System (WMS) that orchestrates all activities.
- AS/RS Miniload: Ideal for manufacturing or distribution operations, Miniload systems provide rapid access to trays or totes of various sizes within a high-density, energy-efficient storage structure.
- Automatic Guided Vehicle (AGV): Perfect for applications involving horizontal transport, material storage and retrieval, inventory management, and replenishment in support of distribution and order fulfillment.
- Pallet Wrapper System: This automated system efficiently prepares pallets for shipment to stores, reducing the labor required to restock store shelves.
- Spiral Conveyor: A solution designed for vertical transport of boxes, totes, and goods of all shapes and sizes across a wide range of industries.
- In-Floor Chain Conveyor: Suitable for high-volume transport over long distances in logistics, cross-docking, distribution, and assembly line operations.
- Vertical Conveyor: The vertical conveyor can be used to quickly and effortlessly transport a wide variety of products to and from any desired height.
- Pallet Chain Conveyor: Chain conveyors are suitable for the horizontal transport of loaded or unloaded pallets.
- Palletizer / Depalletizer: Enhance productivity, save space, and operate 24/7. They can be rapidly integrated into existing workflows and reprogrammed into new flows alongside other equipment.
- Stacker / Destacker: Can be quickly and easily integrated into an existing pallet transport system. Suitable for stacking, separating, or storing standard, unloaded pallets.
- Mobile Pallet Racking: Designed for intensive storage of heavy goods, this system uses a motorized mechanism to move bases along rails embedded in the floor.