Steps to the Future: The Intermediate Level of Automation in Intralogistics and the Role of Dynamic Storage Systems
In an ever-evolving world of logistics, the automation of intralogistical processes is an essential step for companies that want to remain competitive. Warehouse automation is experiencing accelerated growth globally, with the market for automation equipment reaching $29.6 billion in 2024, with growth projections up to $60.04 billion by 2031. Despite this trend, approximately 80% of warehouses worldwide still do not have automated systems, which indicates a huge potential for development.
This article explores the levels of automation in warehouses, with a focus on the intermediate level and the integration of Carton Flow-type dynamic storage systems, a versatile solution that paves the way for progressive automation.
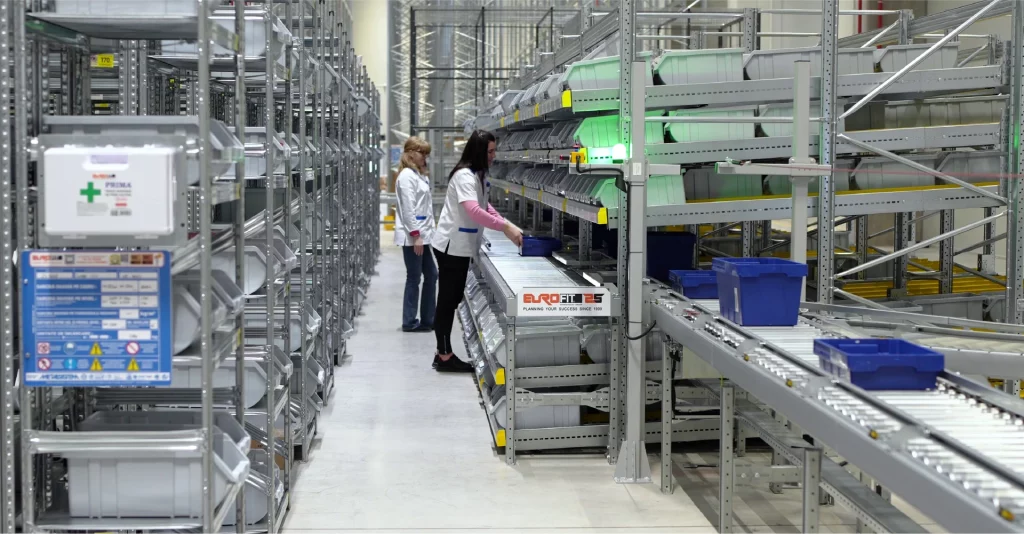
The three levels of automation in intralogistics
Warehouse automation can be implemented gradually, each level bringing specific benefits, with different investment requirements. To better understand the strategic positioning of the intermediate level, it is important to explore all three main levels of automation.
1. Low level
In manual or conventional warehouses, all operations are performed by people, using equipment such as forklifts or lifting/transport equipment. Automation at this level is limited to controlling employees through a warehouse management system (WMS), which takes over the planning, optimization and control of all manual processes. Although it is the starting point for many businesses, this level involves high labor costs, higher error rates and longer delivery times.
2. Intermediate level of automation (partially automated)
The intermediate or partially automated level represents a strategic stage in the evolution of warehouses, where only certain work processes are automated to achieve economical and efficient operations. This hybrid level combines human labor with specific automation technologies, offering a balance between investment and benefits.
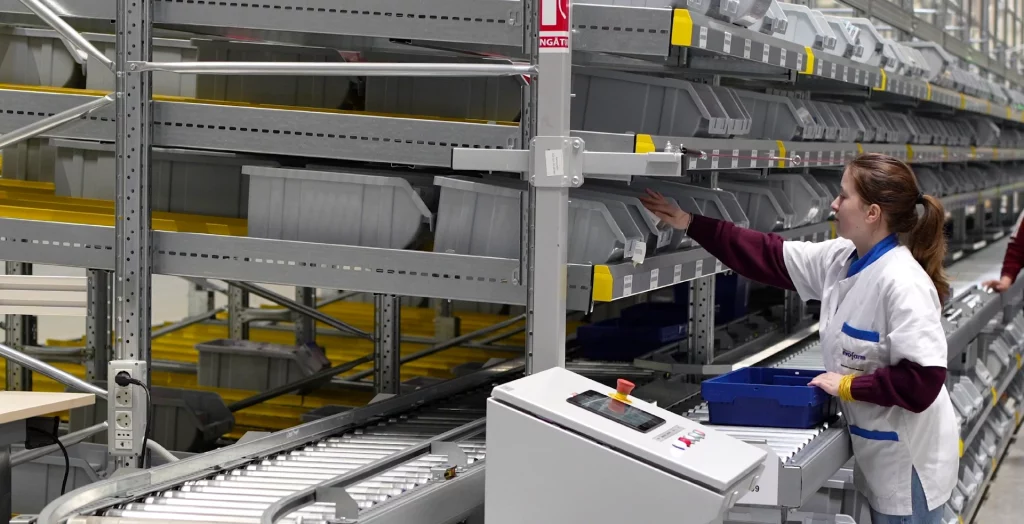
The main characteristics of the intermediate level of automation:
- Assisted picking systems: Technologies such as pick-to-light, voice-picking, or dynamic storage systems that streamline the manual picking process;
- Software-based automation: Using data-driven warehouse control systems (WCS) that help operators coordinate and control warehouse operations;
- Semi-automatic transport elements: Narrow aisle forklifts, picking equipment, and machines with automated navigation systems integrated with the WMS;
- Connectable modules (plug-and-play): Partially automated solutions that can be easily integrated into existing processes and allow flexible expansion as part of a continuous expansion.
At this level, companies can implement specific solutions such as dynamic storage systems, which are an excellent basis for the gradual transition to full automation.
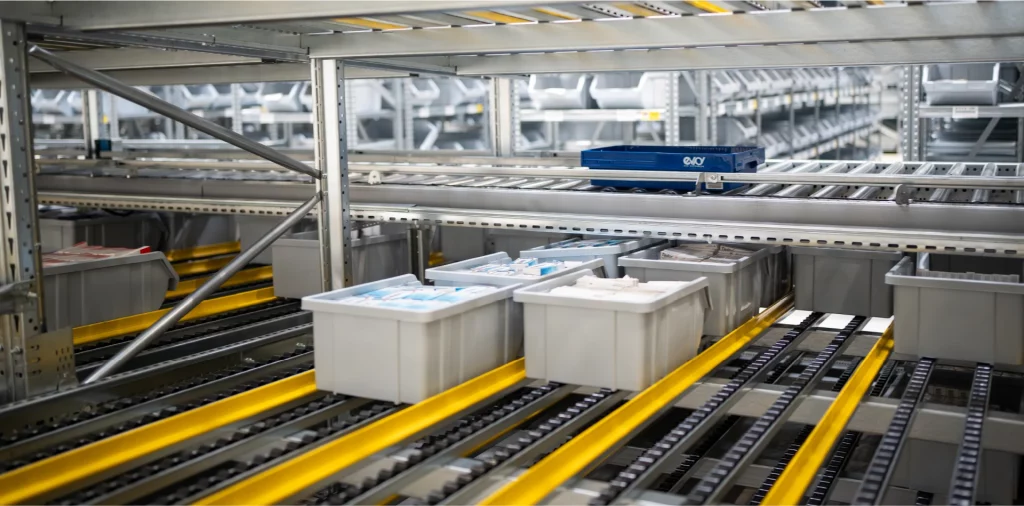
3. Advanced level (fully automated)
Fully automated warehouses represent the pinnacle of intralogistics technology, where most or all processes are performed by robotic systems, with minimal human intervention. These warehouses use advanced technologies such as picking robots, automated guided vehicles (AGV), autonomous mobile robots (AMR), automated storage and retrieval systems (AS/RS), and complex inventory management solutions based on artificial intelligence.
Carton Flow System: The ideal foundation for the intermediate level of automation
One of the systems that stands out at the intermediate level of automation is the Carton Flow (or Live Storage) dynamic storage system. This gravity system allows high-density storage of boxes and light products, generating significant space savings and improved stock rotation control.
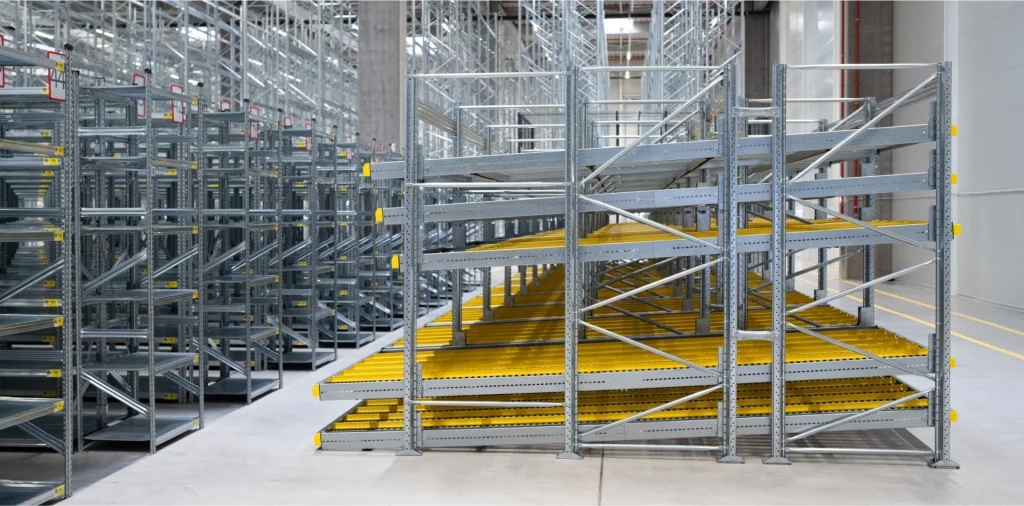
What is the Carton Flow system and how does it work?
The Carton Flow system is a gravity storage system with slightly inclined roller platforms or tracks, where goods are placed at the upper end and move towards the other end by gravity. This operation allows for stock management according to the FIFO (First In, First Out) principle, with the first product in being the first one out.
The operation is simple but efficient: when the first product is removed, the others automatically move to the operator’s position, making it possible to store a large number of items in the same space and significantly reduce handling time.
Key Advantages of the Carton Flow System
- High storage density: Allows for the storage of a large number of products in a small space, reducing the need for a large warehouse footprint;
- Reduced travel distances: The system brings products directly to the operator, reducing travel distances in the warehouse and saving time;
- Increased productivity: Companies that have implemented this system have reported productivity increases of up to 25%;
- Efficient FIFO management: Ensures excellent product rotation and eliminates potential interference;
- Versatility: Șinele pot fi adaptate transversal pentru a acomoda diferite încărcături unitare, făcând sistemul foarte versatil pentru picking;
- Separation of loading and unloading areas: With two clearly separated areas for loading and unloading, the system reduces interference and speeds up the picking process.
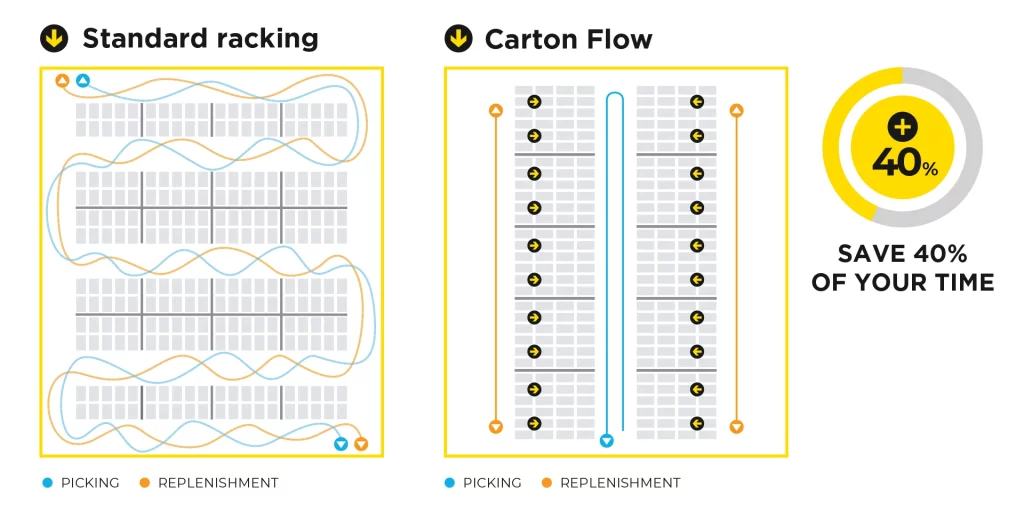
Essential Features of Racking Compatible with the Carton Flow System
To maximize the benefits of the Carton Flow system, it must be integrated with robust and versatile industrial shelving solutions. The ideal shelving structures for this system are made of high-strength galvanized structural steel, certified according to EN10204 standards.
Caracteristici esențiale ale rafturilor compatibile cu sistemul Carton Flow
- Optimized and resistant profiles: Structures with unique column profiles, optimized for transport and installation, with a 50mm pitch for maximum adjustability;
- Structural components made of high-strength steel: Ensures the stability and durability required for dynamic Carton Flow systems;
- Wide range of standardized accessories: Allows for customized configuration for various applications;
- Versatility of application: Adaptability for various types of loads and storage operations.
These racking systems can be used both for implementing Carton Flow at the lower levels and for storing pallets at the upper levels, thus maximizing the use of the warehouse’s vertical space.
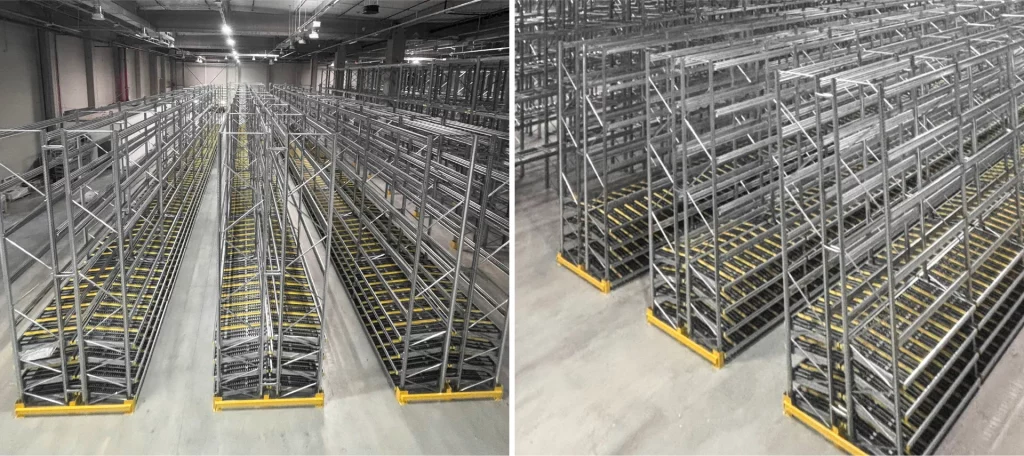
Integrating Carton Flow with Future Automation Solutions
One of the most important qualities of the Carton Flow system is its potential for integration with advanced automation technologies, allowing for a gradual transition to higher levels of automation.
Integration with Transport and Sorting Systems
Carton Flow systems can be connected with conveyors that transport products directly from receiving areas to storage locations or from picking areas to packing and shipping stations. This integration reduces manual handling and increases order processing speed.
Automated sorters can be implemented to direct boxes to the correct channels in the Carton Flow system, automating the replenishment process and ensuring greater accuracy in inventory management.
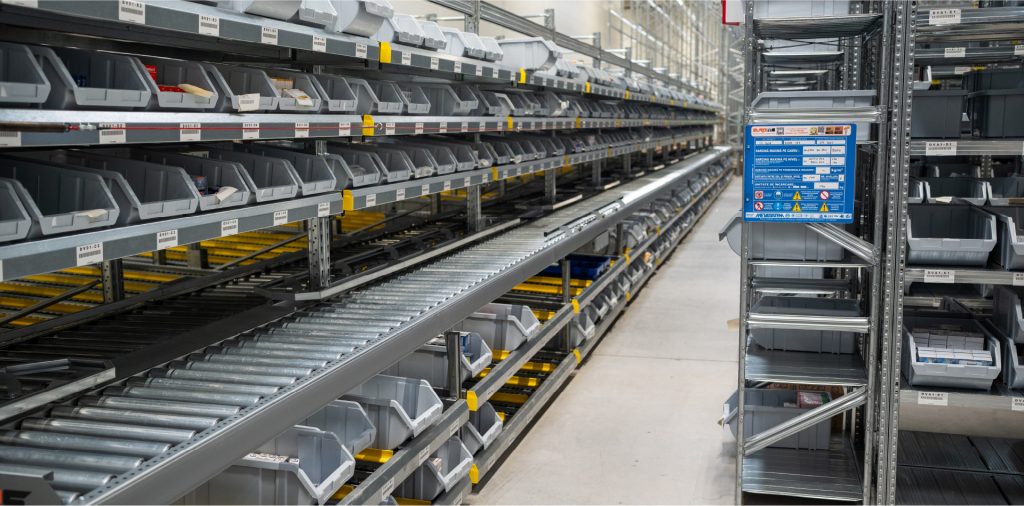
Integration with Autonomous Mobile Robots (AMR)
Autonomous Mobile Robots are a rapidly expanding technology that can perfectly complement Carton Flow systems. AMRs can be used for:
- Automated material transport: Transporting boxes from receiving to Carton Flow storage areas;
- Automated replenishment: AMRs can deliver new products to refill Carton Flow channels when they reach minimum levels;
- Order consolidation: After picking, AMRs can collect products and transport them to packing stations.
Implementing a combined automated storage system for boxes with goods-to-person picking methods can lead to a 25% increase in productivity and allow for order delivery within 24 hours for a catalog of 10,000 SKUs.
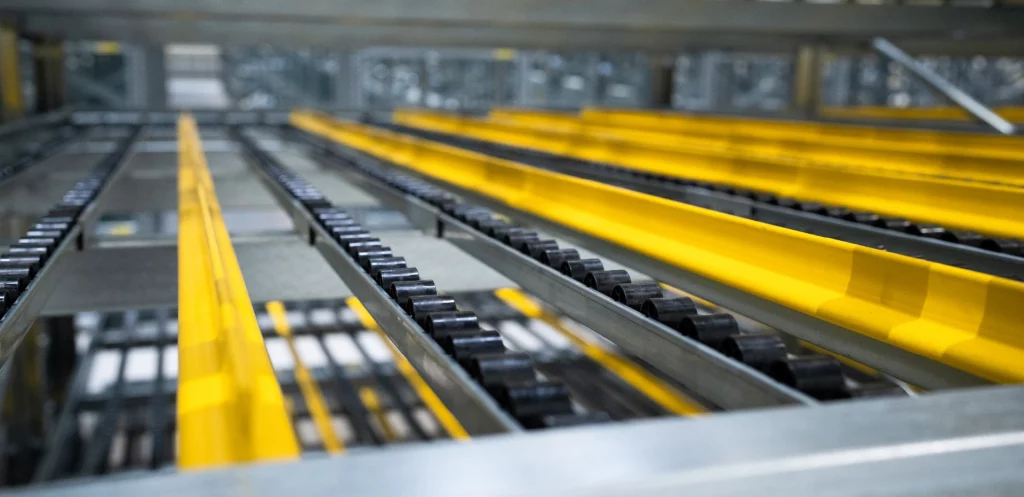
Preparing for the Future of Automated Logistics
The warehouse automation market will experience accelerated growth in the coming years, with projections indicating strong growth. In this context, investments in intermediate automation solutions such as the Carton Flow system represent not only an immediate improvement in operations but also a strategic preparation for the future.
Key Trends for 2025
- Increased adoption of automation: The adoption rate of automation in warehouses has increased from 5% to 25% in the last decade;
- Complete integrated solutions: There is an increasing demand for solutions that integrate hardware and software for scalability and cost savings, solutions that aim to optimize the entire system, ensuring that all components work together efficiently and harmoniously;
- Alternative acquisition models: Services like Robotics as a Service (RaaS) reduce market entry barriers for small and medium-sized companies;
- Artificial intelligence and predictive analytics: Warehouses are becoming increasingly intelligent, using data to optimize operations;
- Cyber-physical automation: By 2027, 75% of warehouses will adopt cyber-physical automation (CPS), which combines physical and digital components to improve operational flows. A cyber-physical system can monitor and create a virtual copy of real-world industrial processes. Thus, we can know the state of each industrial process and control it.
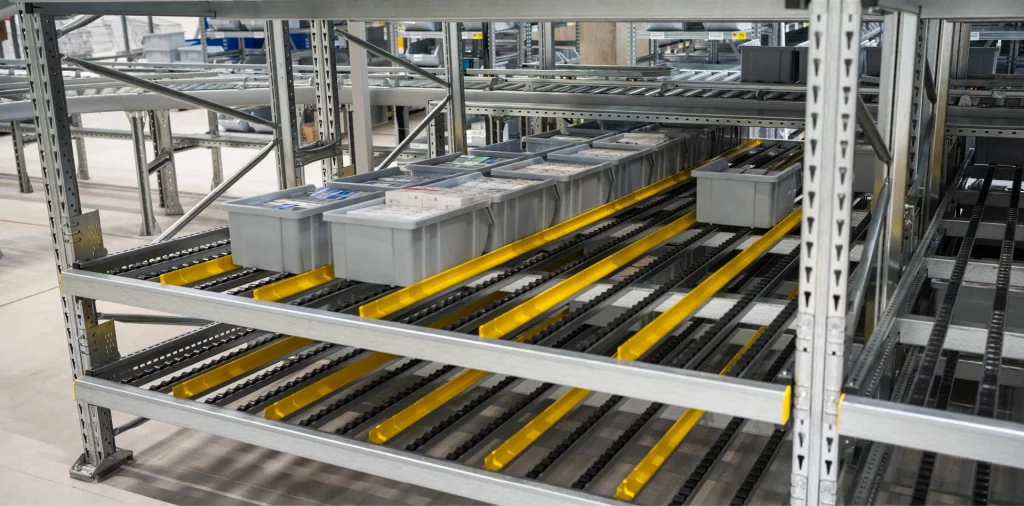
Conclusions: A Gradual Approach to Automation Starts with Carton Flow
For investors looking to optimize their warehouse operations and prepare for the future of automated logistics, Carton Flow systems integrated with robust industrial shelving represent a strategic and calculated first step.
The advantages of this gradual approach include:
- Controlled initial investment: Compared to full automation, intermediate-level solutions like Carton Flow require a much smaller initial investment;
- Immediate results: Significant improvements in productivity and efficiency can be observed immediately after implementation;
- Adaptability to change: Modular systems allow for adjustment and expansion as business needs evolve;
- Risk reduction: A gradual approach reduces the risks associated with implementing a fully automated system;
- Preparation for advanced automation: Creates the operational and cultural foundation necessary for the future integration of more advanced technologies.
Adopting a future-oriented mindset in logistics does not necessarily mean immediately implementing the most advanced technologies available, but building a solid and flexible foundation that allows for the progressive integration of new technologies. The Carton Flow system, combined with robust industrial shelving, represents exactly this foundation – a calculated and strategic step towards the automated future of intralogistics.